Understanding the Role of a Lathe Turning Parts Factory in Modern Manufacturing
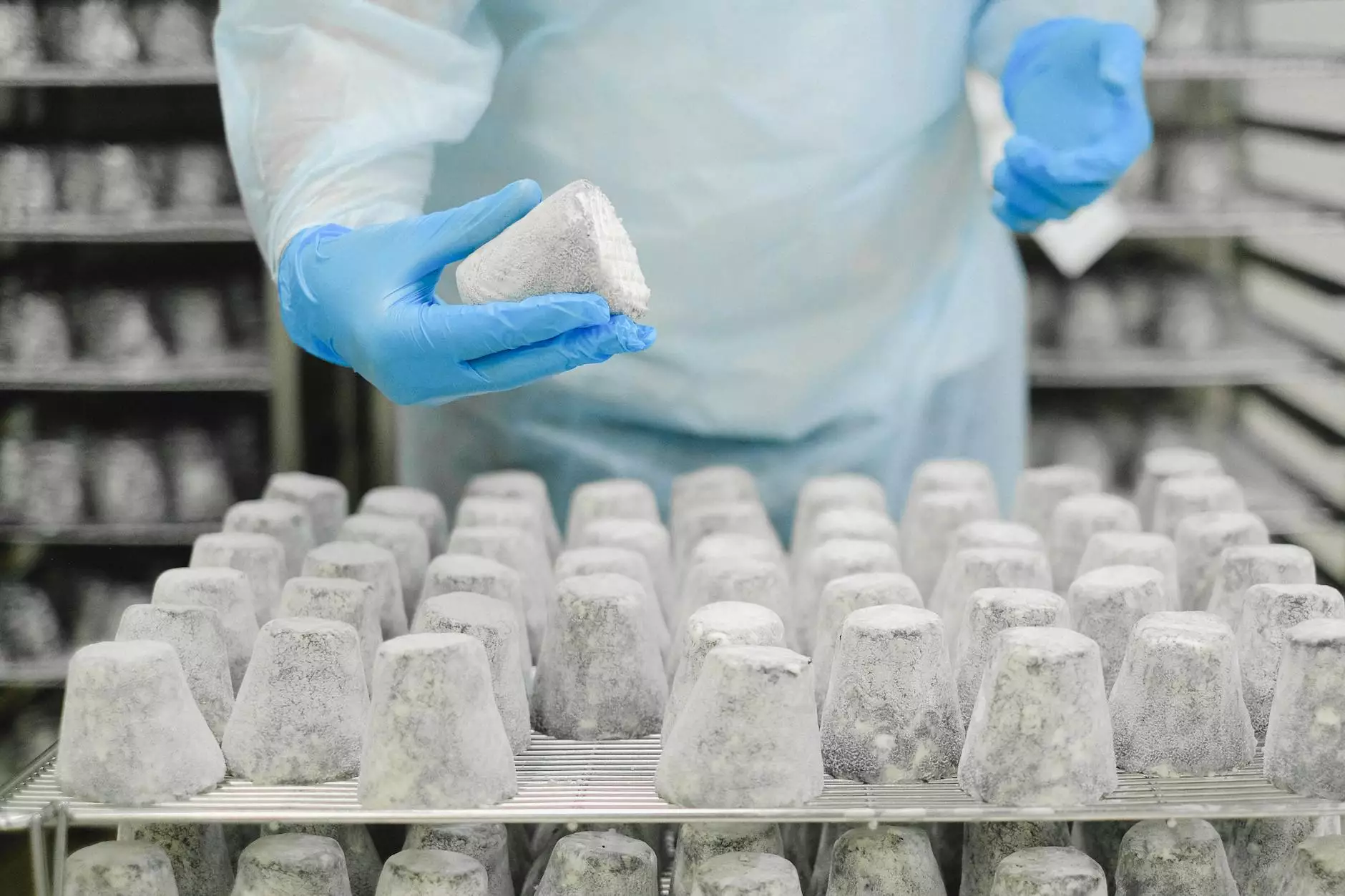
The manufacturing landscape today has witnessed immense evolution, thanks to technological advancements and innovative methodologies. Among the pivotal players shaping this industry, a lathe turning parts factory stands out as a cornerstone for producing high-precision components. This article delves into the intricate workings, advantages, and significant impact of lathe turning processes in metal fabrication, showcasing why these factories are integral to modern industry.
What is a Lathe Turning Parts Factory?
A lathe turning parts factory specializes in manufacturing components by employing lathe turning techniques. This process involves rotating a workpiece against cutting tools to achieve specific shapes and dimensions. The result is precision-engineered parts that meet exact specifications required across various sectors including automotive, aerospace, and industrial machinery.
The Basics of Lathe Turning
Lathe turning is a fundamental machining process where material is removed from a solid workpiece. The lathe itself is a versatile machine that can be used for several machining operations, including:
- Turning: The primary operation that involves removing material to create cylindrical shapes.
- Facing: Trimming the ends of the workpiece to ensure a flat surface.
- Drilling: Producing holes in the workpiece for various applications.
- Threading: Creating helical grooves for screws and bolts.
Advantages of Using a Lathe Turning Parts Factory
Choosing a lathe turning parts factory offers numerous advantages for businesses, particularly in achieving efficiency, quality, and cost-effectiveness in production. Some of the primary benefits include:
1. Precision Manufacturing
One of the standout attributes of lathe turning is the high precision it offers. Factories equipped with advanced CNC (Computer Numerical Control) lathe machines can produce parts with tolerances as tight as ±0.001 inches. This precision is critical in industries where even the slightest deviation can lead to significant operational issues.
2. Versatility
Lathe machines can handle a broad range of materials, including various metals like steel, aluminum, and titanium, as well as plastics. This versatility extends to the complexity of parts that can be manufactured, from simple components to highly intricate shapes.
3. Cost-Effectiveness
Investing in a lathe turning parts factory can lead to considerable cost savings. Mass production capabilities allow factories to produce large volumes of parts quickly, reducing the cost per unit. Additionally, the reduced material waste due to accurate machining makes lathe turning an economically favorable option.
4. Enhanced Surface Finish
Lathe turning not only shapes parts but also enhances the surface finish, making components suitable for both functional and aesthetic purposes. Utilizing advanced tools and techniques, a high-quality surface finish can significantly reduce the need for additional processing.
Key Industries Benefiting from Lathe Turning Parts Production
The benefits of lathe turning extend across various industries, making it a crucial manufacturing process. Here are some key sectors that leverage the capabilities of lathe turning parts factories:
Aerospace Industry
The aerospace industry demands the highest standards of quality and precision. Components such as rotor shafts, fuel nozzles, and landing gear mechanisms are manufactured using lathe turning techniques to ensure safety and reliability.
Automotive Industry
In the automotive sector, lathe turning is crucial for producing parts like crankshafts, timing gears, and brake components. With the push for lighter yet stronger materials, manufacturers increasingly rely on lathe turning to create efficient designs that adhere to performance standards.
Medical Device Manufacturing
Precision is vital in the manufacturing of medical devices. Lathe turning plays an indispensable role in producing components such as surgical instruments and implantable devices, where strict tolerances and biocompatibility are imperative.
Technology and Innovation in Lathe Turning
The landscape of lathe turning is continuously evolving, driven by advancements in technology. Modern CNC lathes utilize sophisticated software for programming complex operations, enhancing both productivity and accuracy.
Automation and Smart Manufacturing
With the advent of Industry 4.0, factories are increasingly integrating automation and smart manufacturing technologies. This integration allows for real-time monitoring, predictive maintenance, and data analytics, optimizing production cycles and reducing downtime.
Adaptive Machining
Adaptive machining technologies enable lathe machines to make adjustments on-the-fly based on real-time feedback. This capability enhances accuracy and helps maintain quality control throughout the production process, ensuring that every part meets the requisite specifications.
The Future of Lathe Turning Parts Factories
As industries evolve, so too do the practices within a lathe turning parts factory. Future developments may include:
- Increased Use of AI: Artificial intelligence will likely revolutionize how lathe operations are monitored and optimized, enhancing efficiency and decision-making.
- Sustainability Efforts: As sustainability becomes a priority, factories will focus on minimizing waste and energy consumption while maximizing recycling efforts.
- Greater Customization: Demand for tailored parts is rising. Future factories will offer more customizable solutions while maintaining efficiency.
Conclusion
In wrapping up, the significance of a lathe turning parts factory cannot be overstated. These facilities are pivotal in driving innovation and efficiency across numerous sectors. With a commitment to precision, versatility, and continually evolving technologies, lathe turning remains at the forefront of manufacturing. For businesses looking to thrive in competitive markets, forging strong partnerships with a reputable lathe turning parts factory like Deep Mould is essential. As the landscape of manufacturing continues to change, embracing these advancements will undoubtedly yield long-term benefits and success.
Contact Deep Mould for Your Lathe Turning Needs
For businesses looking for high-quality, precision-engineered parts, Deep Mould is a trusted partner. With years of experience in metal fabrication, we guarantee top-notch service and products aligned with your specifications. Reach out today to learn more about our offerings.