Understanding the Low Pressure Casting Process: A Comprehensive Guide
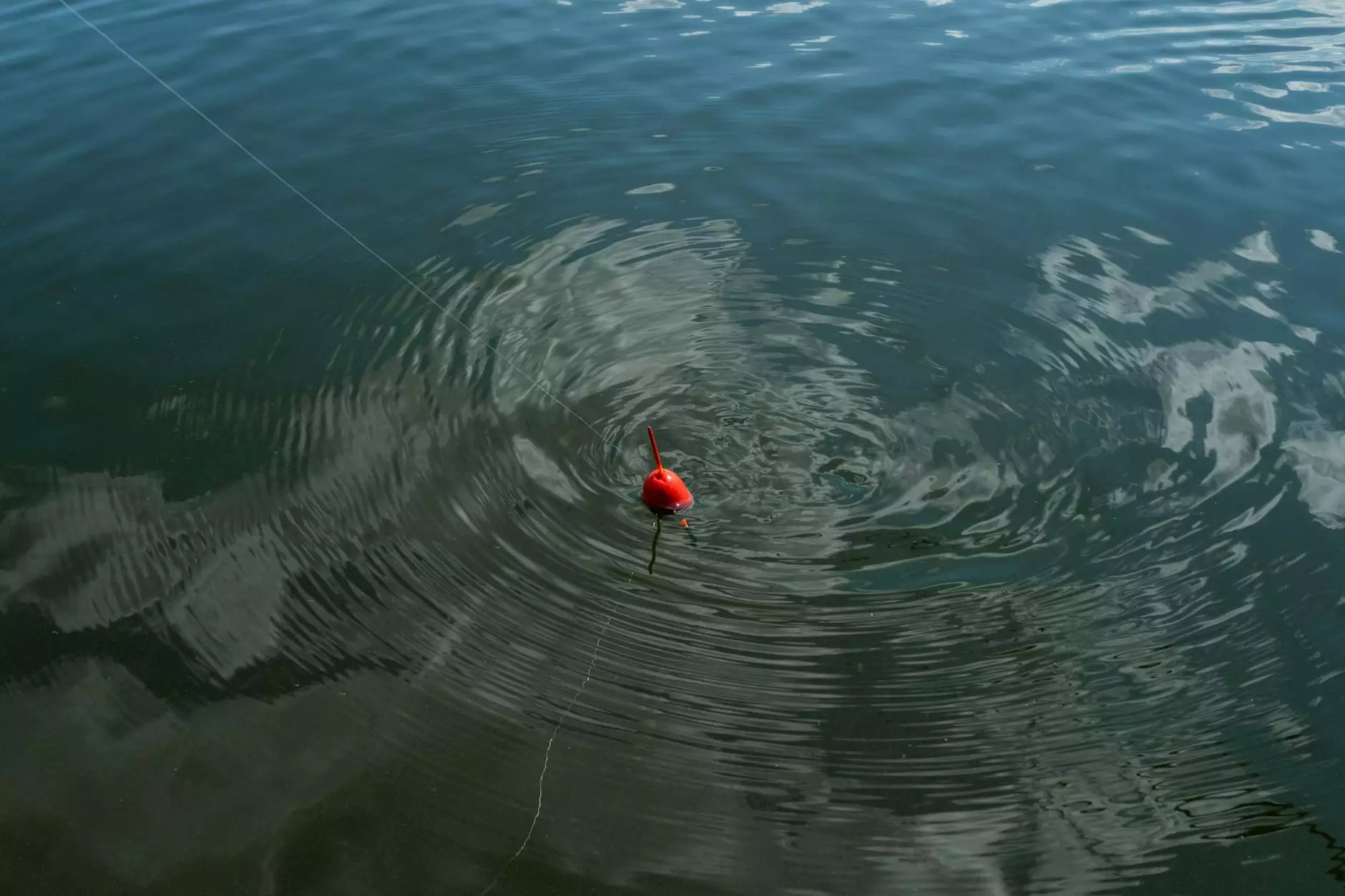
The world of manufacturing is filled with various techniques, each designed to meet the unique requirements of different products. One such technique that has gained significant attention and utilization in recent years is the low pressure casting process. This method is renowned for its ability to produce high-quality castings with enhanced precision and reduced material waste. In this article, we will delve deep into the intricacies of the low pressure casting process, uncovering its benefits, applications, and relevance in fields like art supplies, product design, and 3D printing.
What is the Low Pressure Casting Process?
The low pressure casting process is a unique manufacturing technique that involves pouring molten metal into a mold under low pressure. This method stands in contrast to traditional gravity casting methods, wherein the metal flows freely into the mold without external pressure. The result is a casting that is not only more uniform and defect-free but also features superior mechanical properties.
How Does It Work?
The low pressure casting process can be broken down into several key steps:
- Mold Preparation: The process begins with creating a mold, typically made from materials like steel or aluminum. This mold is designed to withstand the high temperatures of molten metal and is meticulously crafted to ensure precision in the final product.
- Heating: The metal, often aluminum or magnesium due to their favorable properties, is heated in a furnace until it reaches a molten state.
- Low Pressure Application: Once the metal is molten, it is transferred to a chamber where low pressure is applied, typically ranging from 0.1 to 0.5 bar. This pressure forces the metal into the mold, allowing it to fill all intricate details effectively.
- Cooling and Solidification: After the mold is filled, the metal is allowed to cool. The low pressure ensures that any potential gas bubbles are eliminated, leading to denser and more durable castings.
- Extraction: Once solidified, the finished product is removed from the mold, often requiring additional finishing processes to achieve the desired surface quality and dimensions.
Advantages of the Low Pressure Casting Process
The low pressure casting process offers a multitude of benefits that make it an attractive choice for manufacturers across various industries:
- Improved Dimensional Accuracy: The application of pressure in this casting process allows for better filling of the mold, resulting in tight tolerances and precise dimensions.
- Reduced Porosity: Unlike traditional casting methods, the low pressure technique significantly reduces the porosity of the final product, enhancing its strength and durability.
- Material Efficiency: By minimizing waste, the low pressure casting process is more resource-efficient, leading to cost savings for manufacturers.
- Versatility: This process can be used for a wide range of materials and designs, adapting to different industry needs effectively.
- Enhanced Surface Finish: Products produced through low pressure casting often require minimal post-processing, thanks to the smooth surface finish achieved during casting.
Applications of Low Pressure Casting
The low pressure casting process finds its applications in several industries, each utilizing its unique advantages:
1. Automotive Industry
In the automotive sector, manufacturers rely on low pressure casting for components such as engine blocks and transmission housings due to their need for strength and lightweight properties.
2. Aerospace Industry
The aerospace industry benefits from low pressure castings to produce high-performance parts that must meet stringent weight and strength requirements while ensuring reliability in demanding conditions.
3. Art Supplies
For professionals in the arts, the low pressure casting process is essential in creating durable and intricate pieces of equipment and tooling, allowing for both creativity and precision in art supplies.
4. Product Design and Prototyping
Designers frequently utilize low pressure casting for prototypes, enabling them to quickly create functional models that illustrate their ideas accurately and affordably.
5. 3D Printing
With the rise of 3D printing, the low pressure casting method complements additive manufacturing by providing a way to produce high-precision parts that can be directly integrated into 3D printed assemblies.
Choosing the Right Casting Method for Your Project
When it comes to selecting the appropriate casting method for your project, several factors should be considered:
- Material Requirements: What materials are best suited for your product? Consider aluminum or magnesium for their lightness and strength.
- Production Volume: The low pressure casting process is particularly beneficial for medium to high volume production runs, making it ideal for many commercial applications.
- Cost Considerations: Analyze the total cost of production, including material and operational costs, to determine the most economical choice.
- Detail and Precision: If your product requires intricate designs or precise dimensions, low pressure casting is often the best option.
Conclusion
The low pressure casting process represents a significant advancement in casting technology, providing notable advantages in quality, efficiency, and versatility. As industries continue to evolve, embracing these modern manufacturing techniques will be crucial for maintaining competitiveness. Whether you are involved in automotive manufacturing, aerospace engineering, artistic endeavors, or innovative product design, understanding and leveraging the low pressure casting process will undoubtedly enhance your capabilities and outcomes.
At arti90.com, we are committed to offering high-quality products and services that utilize the latest advancements in manufacturing technology, including low pressure casting. Explore our wide range of art supplies, product design solutions, and 3D printing services to elevate your projects to new heights.